Do you know Faucet Casting?
The manufacturing process of the faucet body has four major categories: sand casting, manual metal mold casting, gravity pouring machine and low pressure casting, through which one of the processes is used to manufacture the faucet embryo and carry out the post-casting cleanup as well as the casting inspection.
The general faucet is cast using sand mold casting, also known as sand casting. This production process casting faucet structure will be relatively sparse, very easy to form trachoma and porosity, product quality is difficult to guarantee.
High-end faucet is the use of gravity casting, this production process of casting the internal structure of the faucet is tight, the quality of the product is better than the sand casting. More advanced faucets are die-casting, that is, a one-time pressure grinding molding.
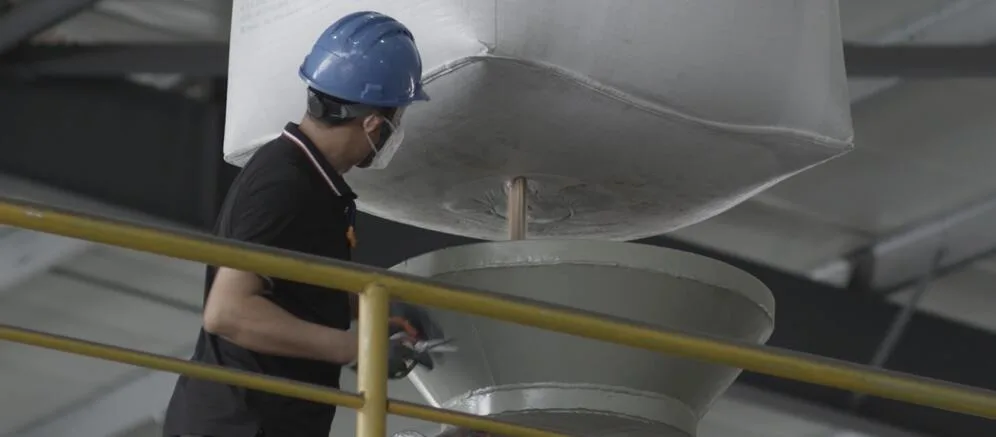
What is the sand turning process like for a regular faucet?
Sand mold casting: the casting method of compact molding with sand. With a variety of shapes, sizes and a variety of commonly used alloy castings for the production of equipment investment is small, raw materials are easy to obtain and inexpensive.
Sand casting is a kind of sand as the main modeling material, the production of casting the traditional casting process. Sand casting is generally used in gravity casting, with special requirements can also be used in low-pressure casting, centrifugal casting and other processes. Sand casting adaptability is very wide, small pieces, large pieces, simple pieces, complex pieces, single pieces, large quantities can be used. Sand casting molds, used to be made of wood, commonly known as wood mold.
Later, the casting factory to change the wooden mold easy to deformation, easy to damage and other shortcomings, in addition to single piece production of sand castings, all changed to higher dimensional accuracy, and longer service life of aluminum alloy molds or resin molds. Although the price has increased, but still cheaper than metal casting molds, in small quantities and large production, the price advantage is particularly prominent.
In addition, the sand type than the metal type fire resistance is higher, so such as copper alloys and ferrous metals and other materials with high melting points are also used in this process. However, sand casting also has some shortcomings: because each sand casting can only be poured once, get casting casting that is damaged, must be re-modeling, so the production of sand casting teach rate is low.
And because of the overall nature of the sand is soft and porous, so the sand casting castings lower dimensional accuracy, the surface is also rougher, however, modern technology has greatly improved the surface condition of the sand castings, the effect of polishing can be comparable with the metal castings.
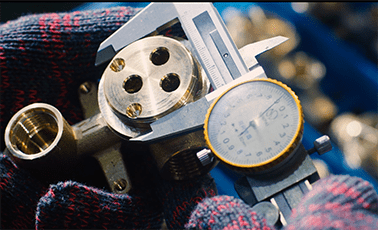
It is worth noting that a variety of chemical bonded sand flourished, clay wet sand is still the most important modeling material, its wide range of application, consumption of large, is any other modeling material can not be compared with it.
What is sand casting?
“Sand casting” when the first half-type on a flat plate, put the sand box to fill the sand to tighten and scrape flat, under the type of manufacturing is complete, will create a good sand mold turned 180 degrees, put the upper half-type, sprinkle the parting agent, put on the sand box, fill the sand and tighten and scrape flat, will be on the sand box turned 180 degrees, respectively, take out the upper and lower half-type, and then the upper type turned 180 degrees and the lower model Combined, sand molding is completed, waiting for casting. This process is commonly known as “sand turning”.
Sand turning is a production method in which molten metal is poured into the casting cavity and cooled and solidified to obtain a product. In the faucet manufacturing process, cast iron is used to make blanks, and sand molding is usually used to manufacture cast iron parts. The raw material of sand mold is mainly sand, and mixed with binder, water and so on.
The sand molding material must have a certain bonding strength in order to be molded into the desired shape and to be able to withstand the washout of hot copper water without collapsing. In order to create a cavity within the sand mold that matches the shape of the casting, a model must first be made from wood, called a wood mold.
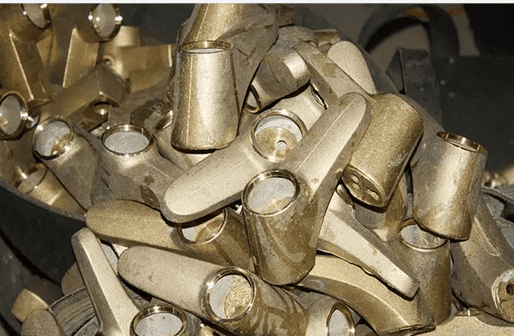
The volume of the hot copper water will shrink after cooling, therefore, the size of the wooden mold needs to be increased according to the shrinkage rate on the basis of the original size of the casting, and the surface that needs to be cut and processed is thickened accordingly. Hollow castings need to be made of sand core and the corresponding core wooden mold (core box). With a wooden mold, you can turn the cavity sand mold.
In the manufacture of sand mold, to consider how to separate the upper and lower sand box in order to take out the wooden mold, but also to consider where the copper water from the inflow, how to fill the cavity in order to get a good quality castings. After the sand mold is made, it can be poured, that is, the copper water is poured into the cavity of the sand mold. Then there are also sand removal, repair, polishing and other processes, to become a qualified faucet body.
Sand casting has a long history and is the most widely used process. Speaking of long history, can be traced back to thousands of years ago; on the scope of its application, it can be said that there is no place around the world do not use.
Summary
If you want to know more please click:https://infaucets.com